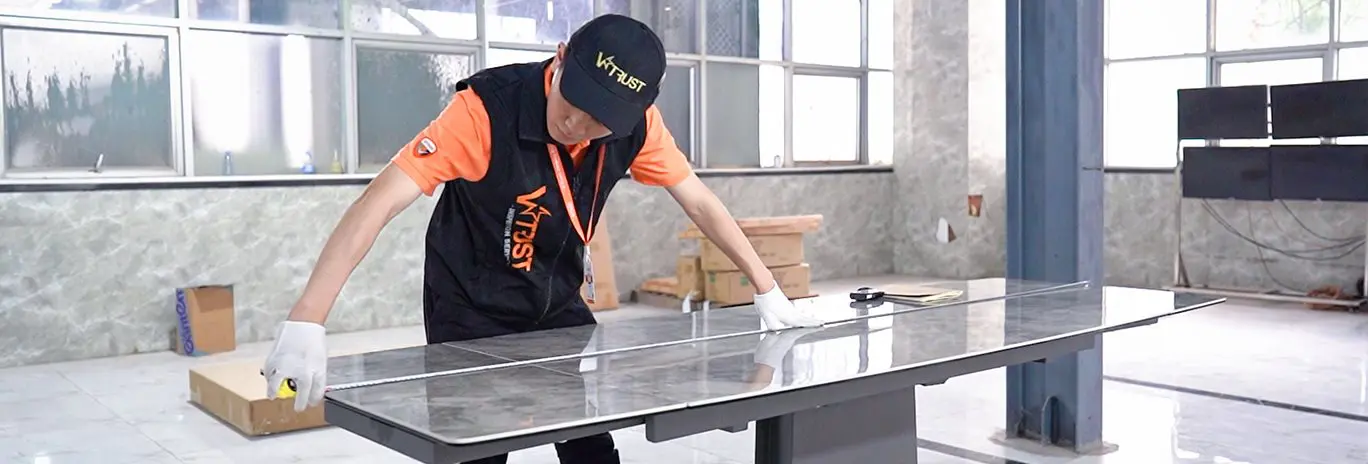
Quality Control Services for Furniture in Asia including China, Vietnam, India, Bangladesh, Thailand, Malaysia, Indonesia, Cambodia, Myanmar and Pakistan
V-Trust's inspection services for furniture products ensure that items meet customer specifications and quality standards through a thorough evaluation of product workmanship, performance and functional testing, as well as packaging conditions, marking, and labeling.
Supported by over 460 full-time inspectors, including a dedicated team of technical managers and inspection engineers, V-Trust ensures that goods strictly adhere to buyers’ quality plans, drawings, and contractual specifications.
What Are the Products We Inspect?

Home Furniture
- Sofas & Beds
- Chairs & Stools
- Tables & Desks
- Drawers & Cabinets
- Children Furniture
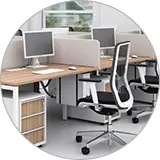
Office Furniture
- Office Desks
- Conference Tables Office
- Chairs
- Shelves & Cabinets
- Cubicle Systems
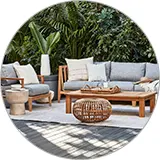
Outdoor Furniture
- Rattan Furniture
- Patio Sets
- Picnic Tables
- Hammocks & Swings
- Sunbeds & Umbrellas
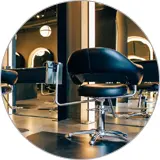
Commercial Furniture
- Hotel Projects
- Restaurant Sets
- Cafes & Bars
- Hospital Furniture
- Classroom Furniture
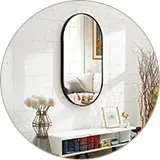
Home Furnishings
- Mirrors & Frames
- Curtains & Blinds
- Rugs & Runners
- Mattresses
- Cushions
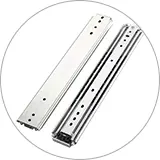
Furniture Accessories
- Casters
- Chair Mechanisms
- Swivel Plates
- Chair Pads
- Floor Protection
What’s Covered in a Product Inspection for Furniture Products?
V-Trust has more than 2.500 checklists based on specific product type. Our general checklist for on-site inspection of furniture and home furnishings includes the following criteria:
- Quantity check
- Color comparison
- Size & weight
- Assortment check
- Product appearance
- Barcode scanning
- Assembly test
- Stuffing check
- Packing check
- Stability test
- Fitting check
- Carton drop test
- Loading test
- Zipper & accessories check
- Unit drop test
- Impact test
- Finger entrapment check
- Instruction manual
- Fatigue test
- Tempered glass check
- Mold prevention
- Humidity test
- Coating adhesion
- Cut prevention
- Wobble test
- Smell test
- Damage prevention
In addition to the above aspects, we can also carry out a tailor-made checking plan according to your own testing plan and inspection requirements.
Furniture & Home Furnishings Common Defects Found During Product Inspections
Function
- Wobble
- Slant surface
- Deformation
- Noise during use
- Poor assembly
Appearance
- Sharp edge / sharp point
- Splinter
- Chip / Crack
- Rust / oxidation
- Poor polishing
Specification
- Misalignment
- Tipping over
- Slanted holes
- Wrong component size
- Wrong accessories size
Safety
- Mildew
- Splinter
- Exposed nail
- Sharp point/edge
- Loose component
Packing
- Carton damage
- Missing component
- Incorrect warning
- Incorrect marking
- Empty space in cartons
Material
- Wrong material
- Rough material
- Mold mark
- Deformed tube
- Collapsing panel
Supplier Evaluation for Furniture & Home Furnishing Products
Factory Audit for the furniture manufacturers is the evaluation of supplier according to industry standard and your requirements. During the audit, V-Trust auditor checks whether the factory has main certificates for furniture manufacturing, such as FSC certificate & ISO 9001:2015, quality certificates for the raw materials and main business & export documentation, and verifies your supplier’s capabilities, systems, management, and operating procedures.
Generally, during the factory audit we will focus on the following aspects:
- Company profile (General information)
- Production process
- Facilities & machinery
- R&D
- Organization structure
- Production capacity
- Quality assurance system
- Special Requirements from Client
Laboratory Testing for Furniture Products
Furniture and Home Furnishing products are required to comply with necessary regulations & testing standards, and here in V-Trust we help to support you with independent sample selection from production, and testing arrangements in our own laboratory.
- REACH SVHC(Metal & Non-Metal)
- CPSIA(Lead, Phthalates, Formaldehyde, Heavy metals, Cadmium, Mercury, Nickel)
- PCP
- ASTM B117 - Salt Spray Test
- EN 71, EN 1103, ASTM F963, CFR(Flammability testing)
- Material Chemical Composition Analysis
- OEKO-Tex 100 Azo dyes
Frequently Asked Questions on Inspection of Furniture
Why do I need shipment inspection for furniture?
Will you assemble furniture samples during the inspection?
How many days in advance should I book the inspection?
Who will I be in contact with throughout the whole process?
Do I need to send you an approved sample?
How many days prior to shipment should the inspection take place?
Can I discuss with you in details about my own inspection criteria?
How long does it take to get my report?
What if I have questions after I receive your report?
Contact us now for more information about quality control or supplier evaluation in Asia.